Nucleus VR – Connecting People and Information Worldwide in Real-Time
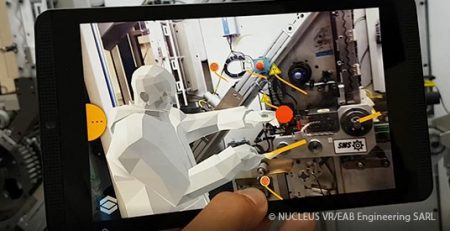
Human survival in space is highly dependent on life support systems, computers and equipment. Maintaining these complex systems requires support of hundreds of earth-based experts. Nucleus VR is removing the distance barrier, by allowing astronauts and experts to work simultaneously, as if they were together in the same place. Experts simply connect to the digital twin of the spacecraft and appear in the real spacecraft as a holographic companion. Data can also be placed on the digital twin and displayed in the real spaceship with Augmented Reality (AR). Thereby, challenges can be solved faster, and in a natural, intuitive and less stressful way.
Benefits:
- Connecting astronauts and experts all over the world in the digital twin
- The digital twin is built from existing CAD data using a simple drag-and-drop process
- Many kinds of data can be pinned to the digital twin (live telemetry streams, PDF, video, 360° video)
- Increase astronauts’ well-being through meetings with family and friends in relaxing virtual worlds
- Compatible with most existing AR/VR (Virtual Reality) hardware: HTC VIVE, OCCULUS, Android AR, castAR, PC, HOLOLENS
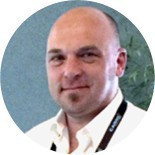
NUCLEUS VR / EAB Engineering SARL
Lyon, France
Alexander Bolton
www.nucleusvr.net
abolton@nucleusvr.net
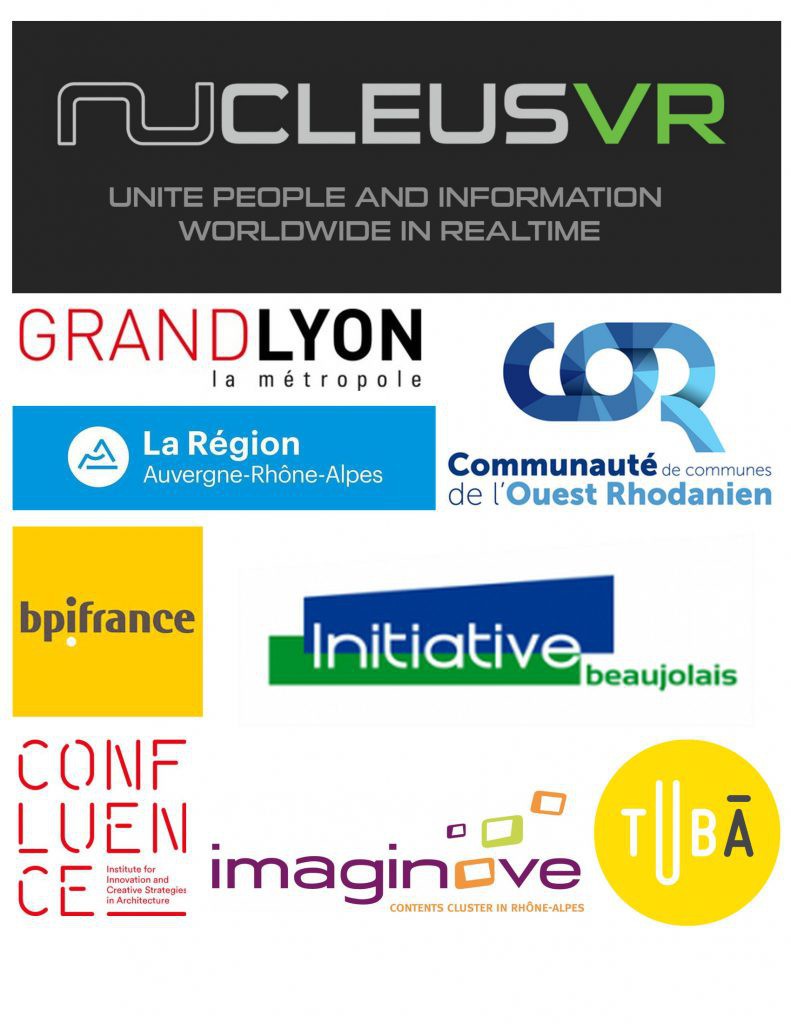